2022 is a landmark year and a huge milestone for Sub-drill. We are proud to celebrate 30 Years in business and would like to take this opportunity to thank our customers, vendors, peers and staff for their valuable support, commitment, and dedication over the years.
From Sub-drill’s incorporation in 1992 with the opening of its first facility in Dyce, Aberdeen, we have continued to grow and develop both in terms of capability and capacity, offering design and manufacture of products which enhance client operations.By collaborating closely with Customers and Partners we have developed a proven product range, earning recognition throughout the global energy industry as a reliable and trusted manufacturer and supplier of subsea gaskets, tools, and drilling equipment.
Sub-drill continues to embrace industry change and advancements in technology. We have made informed decisions over the years allowing us to develop our personnel, build proven “in house” work systems to add value to the business, and invest in purpose-built state-of-the-art design and manufacturing facilities. The completion of a recent 6900 sq. ft extension offers additional footprint to meet our unique procedures and processes and underlines our commitment to the Industry and Sub-drill’s future.
Since 1993, our Sub-X™ Wellhead & BOP System Subsea Gaskets have been used throughout the world wherever deep-sea exploration and production of oil and gas takes place, providing quality, expertise, reliability, consistent performance and zero failure since its introduction.
The completion of a recent R&D programme to qualify our gaskets to the latest API/ISO industry standards, all witnessed by NOBO, further enhances our reputation, and highlights our expertise as a world leading designer and manufacturer of subsea ring gaskets, thus ensuring confidence in the use of our product by a global and growing customer base that seek compliance with the relevant international standards.
A variety of new products have been launched over the years which have become the product of choice for a number of internationally based customers, including our DSV™ Test Stand, MS-V™ Mud Saver, Weight Optimised Integral Lift Bails, and a Flanged design of Side Entry Sub with multiple configurations for a variety of applications to save on cost while maintaining performance. We have also added BOP Test Tools, and a range of Jetting Tools for a variety of applications, and we continue to focus on helping reduce operating costs and increasing efficiencies for rig operators by providing innovation and high-quality product for their operations.
Our product offering is enhanced with design capabilities for manufacturing bespoke tools, along with manufacturing and design project services to a decerning client base, and of course our “in house” repair facility offering inspection, repair, refurbishment, and pressure testing to the latest industry standards for both Well Control Valves including Top Drive, and Rotary Substitute Products.
Since the early days, we have widened our market reach with distribution outlets through reliable and trusted partners in Norway, Brazil, Abu Dhabi UAE, USA, Singapore, and Australia, building a global network for our unique product range.
The ongoing Pandemic has brought its own set of challenges that Sub-drill has met head-on. We have implemented many procedural changes to ensure the safety of our employees while preserving our ability to operate and meet our client's requirements. With reduced face to face business and global travel, we stay connected with our clients and develop new prospects via video conferencing, and to stay ahead of the game, we engage more actively in the digital world. By embracing technology, we will keep everyone informed through our website and by social media about the relevant developments in our business, and innovation in our product lines.
Mark Paton (Managing Director) commented ... "We have gained much respect with our Global client base over the years. Sub-drill has grown in strength, capacity, and capability to the point where its unique product range is now recognised throughout the world by major operators in the Oil & Gas Industry. We are privileged to be seen as a proven and trusted worldwide manufacturer and supplier.
It is incredible but true, Sub-drill opened its doors for business 30 years ago in 1992, it is a milestone that we are all proud of, and one that we are embracing and celebrating as a developing company.
Over the years we have continued to evolve, we have made informed investment decisions along the way, and we fully understand the importance of quality, service and compliance and keep these values at the forefront of everything we do. The professionalism and customer focus of our in-house team has always been integral to our continued success and will continue to be, hopefully for another 30 years to come."
Visions and plans for the future
• Gain additional quality accreditations to improve and enhance our manufacturing capabilities.
• Invest in testing of existing and new product lines to ensure that we continue to meet industry requirements and remain at the forefront of design for products which can be used in ever more severe operational working conditions.
• Continue to invest and train to increase the knowledge base of our staff for both their own benefit as well as for our clients.
• Continue to invest in new technology and product design to maintain competitiveness, offer new solutions, and value for money for our customers.
• Increase global awareness of our company and provide international support for our clients with quality service and quick supply.
1992 / 2022
1992: Sub-drill Supply Limited was incorporated. Sub-drill opened its first workshop facility in Kirkhill Place in Dyce, Aberdeen, offering drilling equipment supply services.
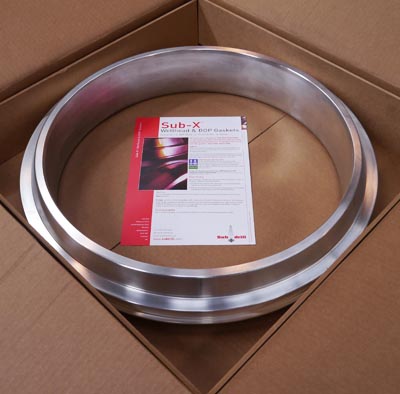
1993: Sub-drill introduced its Sub-X™ OEC Subsea Wellhead & BOP Ring Gasket product line.
1995: Sub-drill was awarded Distributorship for Crestex (now Drillmax), offering drillpipe float valves and spares.
2002: Sub-drill introduced its DSV™ Drill Stem Test Stand product line

2003: Sub-drill introduced its MSV™ Pneumatic Mud Saver line.
2004: Sub-drill was appointed Distributor for the Global Manufacturing range of drill stem valves.
2007: Sub-drill opened in-house Valve Shop, offering the repair, service and test of drill stem valves. Appointed Global Manufacturing’s Service Centre for Europe and Africa in the same year.
2010: Sub-drill purchased a Mazak E500 CNC 5 Axis Multitasking Machine Tool to manufacture its own range of drill stem tools and drilling products.
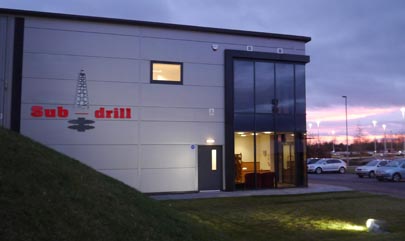
2011: Sub-drill moved to a new purpose built state-of-the-art facility in Arnhall Business Park, Westhill, Aberdeenshire.
2011: Sub-drill purchases a Mazak ST-60 Turning Centre to add capacity, and further enhance its manufacturing capabilities.
2012: Quality Management system accredited by BSI to meet the requirements of ISO 9001: 2008.
2014: Sub-drill built a new extension to incorporate an in-house coating facility and additional storage and packing facilities. The coating facility allows Sub-drill to streamline and better control the silver plating process for its range of Sub-X™ OEC ring gaskets, and the phosphate coating of its increasing range of drilling tools.
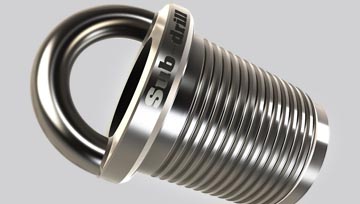
2015: Sub-drill released its new range of weight optimised handle style lift caps. The new product is manufactured from one piece of alloy steel to enhance longevity, quality, and to allow easier handling by rig personnel.
2015: Sub-drill installed a SEIKI Production Planning system to better integrate its production process, providing visual up to date management of its inventory and production processes. This maximised internal efficiencies for both Sub-drill and its customers.
2015: Sub-drill made further investment in its manufacturing capabilities with the purchase of a Mazak NEXUS 450 CNC 3 Axis Multi Tasking Machine Tool.
2016: Sub-drill introduced its Vort-X™ BOP / Wellbore Jetting Tool, developed as the next step in the evolution of effective wellbore cleaning and debris removal. This unique tool is created in conjunction with the Sub-drill field proven Bull Nose Jetting Sub, adding to its range of combination jetting tool products.
2016: Sub-drill gain facility approval by Fearnley Procter as a NS™-1 Level 2 manufacturing facility for its drill stem substitutes range, further promoting its commitment to maintain and improve product quality.
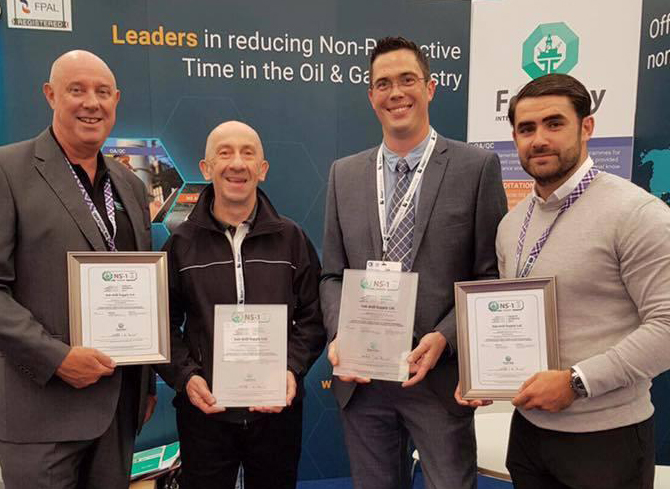
2016: Sub-drill gain facility approval by Fearnley Procter as a NS™-1 Level 2 manufacturing facility for its drill stem substitutes range, further promoting its commitment to maintain and improve product quality.
2016: Sub-drill add design to its ISO scope of services.
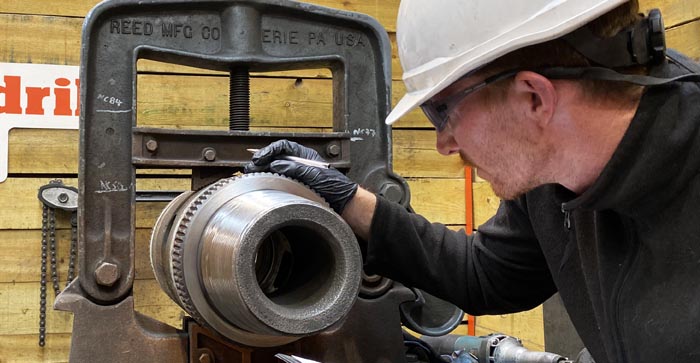
2016: Sub-drill appointed authorised licensee to machine DP-Master Performance Connections.
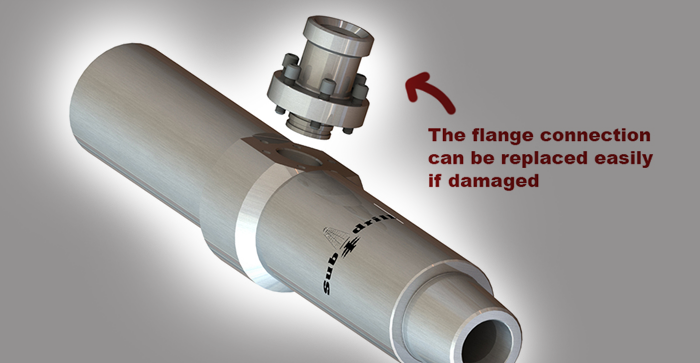
2017: Sub-drill introduced new variant of its flanged design side entry sub with dual angle, to enable remote activation for a variety of operations.
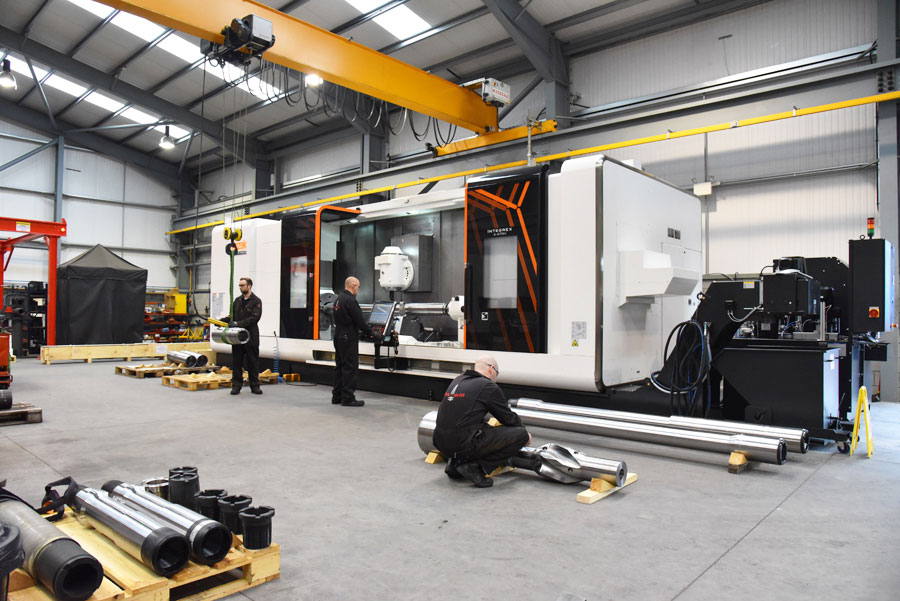
2017: Sub-drill purchased a Mazak E670H CNC 5-Axis Machine Centre to add additional capacity and capabilities to its manufacturing services.
2018: Sub-drill Quality Management System renewal, accredited by BSI to meet the requirements of ISO 9001: 2015.
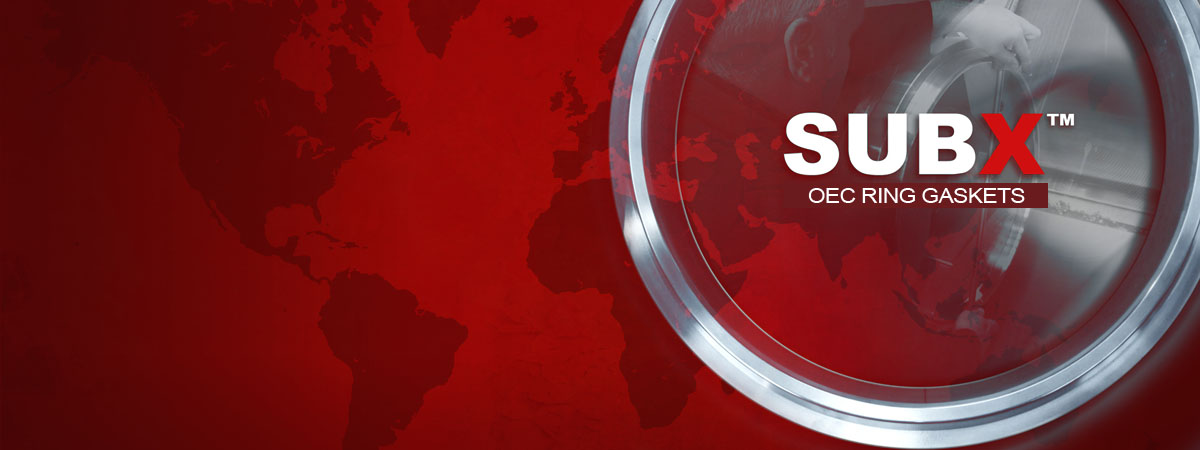
2018: Sub-drill initiated R&D programme to update its Sub-X™ subsea wellhead and BOP ring gasket qualifications.
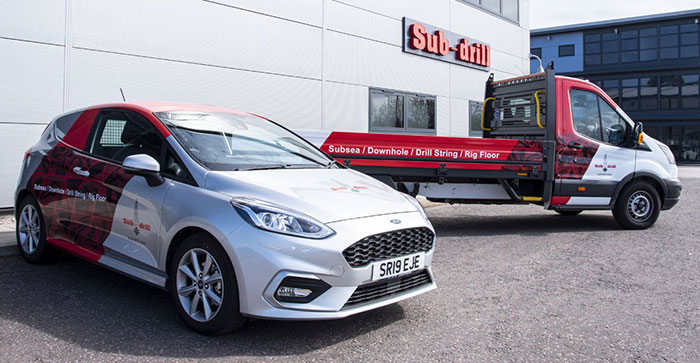
2019: Sub-drill introduced corporate branding on its company vehicles.
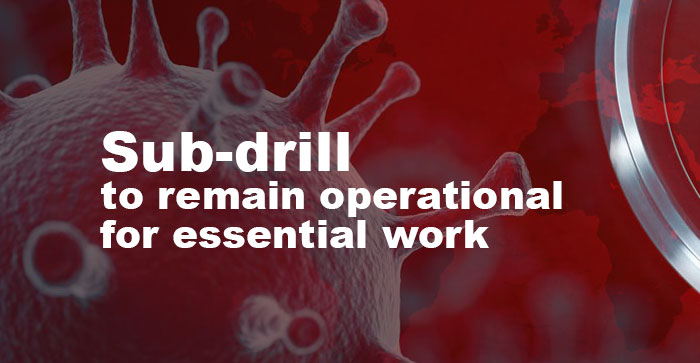
2020: Sub-drill implemented procedural changes internally to keep its employees safe, ensure compliance with Government guidelines, and maintain support for its customers with products and services during the global pandemic.
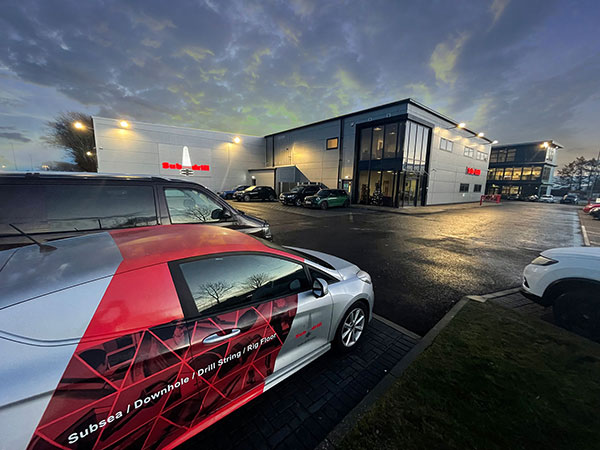
2020: Sub-drill started work on expanding its world class manufacturing facility in Westhill UK with the addition of solar array panels to help lower the company's carbon footprint.
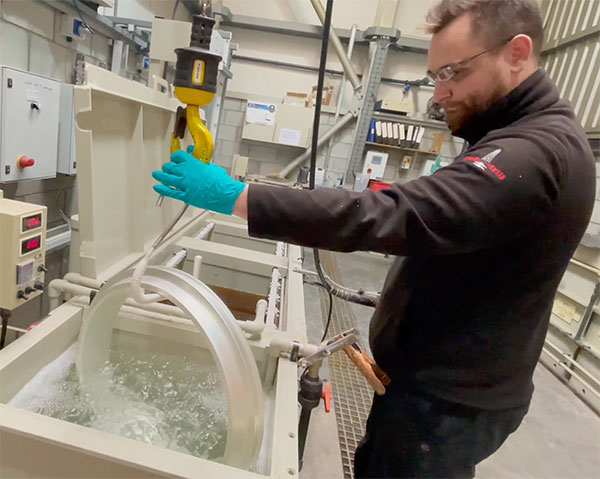